The Real Pet Food Company was offered the opportunity to participate in a duty holder review (DHR) process by WorkSafe, with a view to improve safety at its Christchurch and Auckland factory sites.
The Real Pet Food Company, which acquired the New Zealand business in mid-2017, has 81 staff in New Zealand, with 55 working in the factories producing its range of chilled and frozen 100 per cent meat pet foods. The rest of the team work in sales, merchandising and administration.
The company holds monthly health and safety meetings for its work groups. A H&S committee, made up of staff members with management representation, meets bi-monthly. Health and safety is also addressed at weekly staff toolbox meetings.
Last year an accident occurred at the Christchurch factory, in which a staff member lost the tip of a finger. We have one bandsaw at each of the factories, to cut frozen blocks of meat,” says Real Pet Food Company HR and Safety Specialist Stacey Wyatt.
“It’s a two-man operation. When the meat has passed through the bandsaw, it is picked up by a ‘catcher’ on the other side of the saw and put into a container.
"We were very open to assistance from WorkSafe and Tim’s advice was very good.”
Through a thorough investigation we managed to establish the root cause of the accident and implement corrective action.
“Our safety requirement is that the blocks are picked up singly. However, on this occasion the catcher was picking up two blocks at once in a scooping motion - resulting in the tip of his middle finger coming into contact with the small part of the blade which was not covered by the vertical guard.”
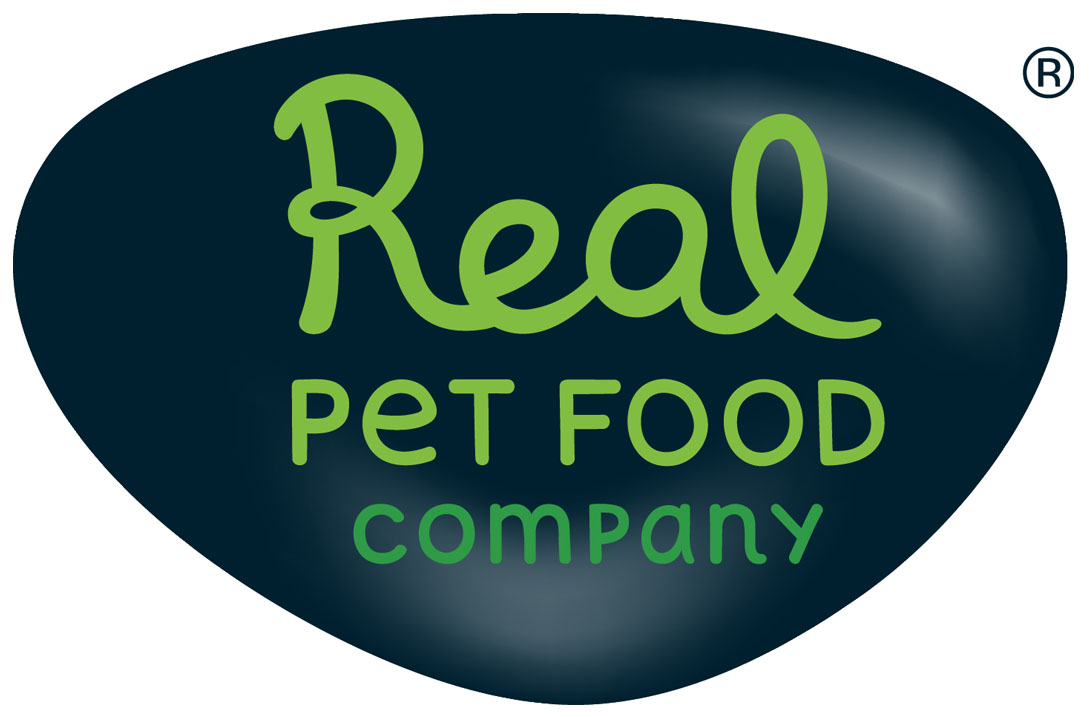
The company notified WorkSafe and, while the accident was below the threshold for formal investigation, it was decided to provide a Duty Holder Review.
“That’s when we contact the business and look at how lessons can be learned to prevent accidents happening in the future,” says Christchurch-based WorkSafe Duty Holder Review Officer, Tim Heyworth.
“Stacey was very open to the process of learning. They had good CCTV footage of the incident and were keen to share that and discuss how they could make their workplace safer. They had already put interim measures into action, including lengthening the bench between the bandsaw and the catcher, to reduce the likelihood of coming into contact with the blade.”
The BladeStop bandsaw, developed by Scott Automation, was designed specifically for the meat industry. It is uniquely designed to reduce risks of serious injury when the unit senses a person has come into contact with the blade. Upon sensing contact, the blade stops operating within 0.009 seconds – the difference between a small skin cut or an amputation.
“I already had experience of working with meat processing companies in implementing BladeStop,” says Tim. “In its early days it was usually too costly for small to medium companies, but it has come down in price.
“I made Stacey aware of the technology and whether they might consider it. The case was then closed – but the company continued with that process.”
“We were very open to assistance from WorkSafe and Tim’s advice was very good,” says Stacey.
“Having been made aware of BladeStop, I discussed it with our team and we decided to put a proposal through to our Australian parent company to see if it was a viable option.
“It was a whole company achievement. We brainstormed it as something we could do to keep our staff safe and we discussed the potential benefits and disadvantages. Our Health and Safety lead in Australia was involved and our Technical Director visited Scott Automation’s Australian site.
“Then the decision was taken to replace both the New Zealand bandsaws and the one bandsaw in Australia with BladeStop technology. These cost $86,000 each, and we replaced a new $25,000 bandsaw we had installed in Auckland just three months before. From the get go, Real Pet Food Company has said health and safety is our number one priority – and it’s great to work for a company that really lives that value.”
Scott Automation provided four hour training sessions for staff in using the new bandsaws, as well as further training for Stacey.
"Our staff really appreciate how the company responds to their concerns.”
“It took a little bit of getting used to and some follow up sessions with me before the guys were fully comfortable with it,” he says.
“However, when you weigh up the personal impacts of an accident, plus the productivity losses, the benefits far outweigh the cost.”
The company has also recently sought advice from WorkSafe to improve safety around traffic management at its Auckland site and implemented a number of measures, including a major project to relocate car parking areas.
“Use of forklifts, and traffic are among our major risks,” says Stacey. “Our staff are very proactive about making the health and safety reps aware of any issues, and this was something which came out of that staff feedback.
“Over 50 years of operation, we have expanded into the site, and staff raised concerns about how close forklifts were getting to people. We worked with them on the best ways to address that and, in response, we have moved a fence, installed barriers and bollards and put down new line markings.
“We also sought advice from Shane Strode-Penny, WorkSafe’s Northern Region Inspector for Auckland, and relocated our car park. That was a major project at significant cost but with important safety outcomes.”
Stacey says both customers and staff are impressed by the company’s proactive approach to health and safety.
“We provide a health and safety induction for everyone who comes onto our sites and visitors often comment that it is the most thorough they have experienced,” he says.
“Our staff really appreciate how the company responds to their concerns. They are very engaged in our ongoing education around health and safety and the technical improvements the business is investing in to drive a safer work environment. It’s very much a two way process."
Related information
Last updated